La diffusion de l’infusion
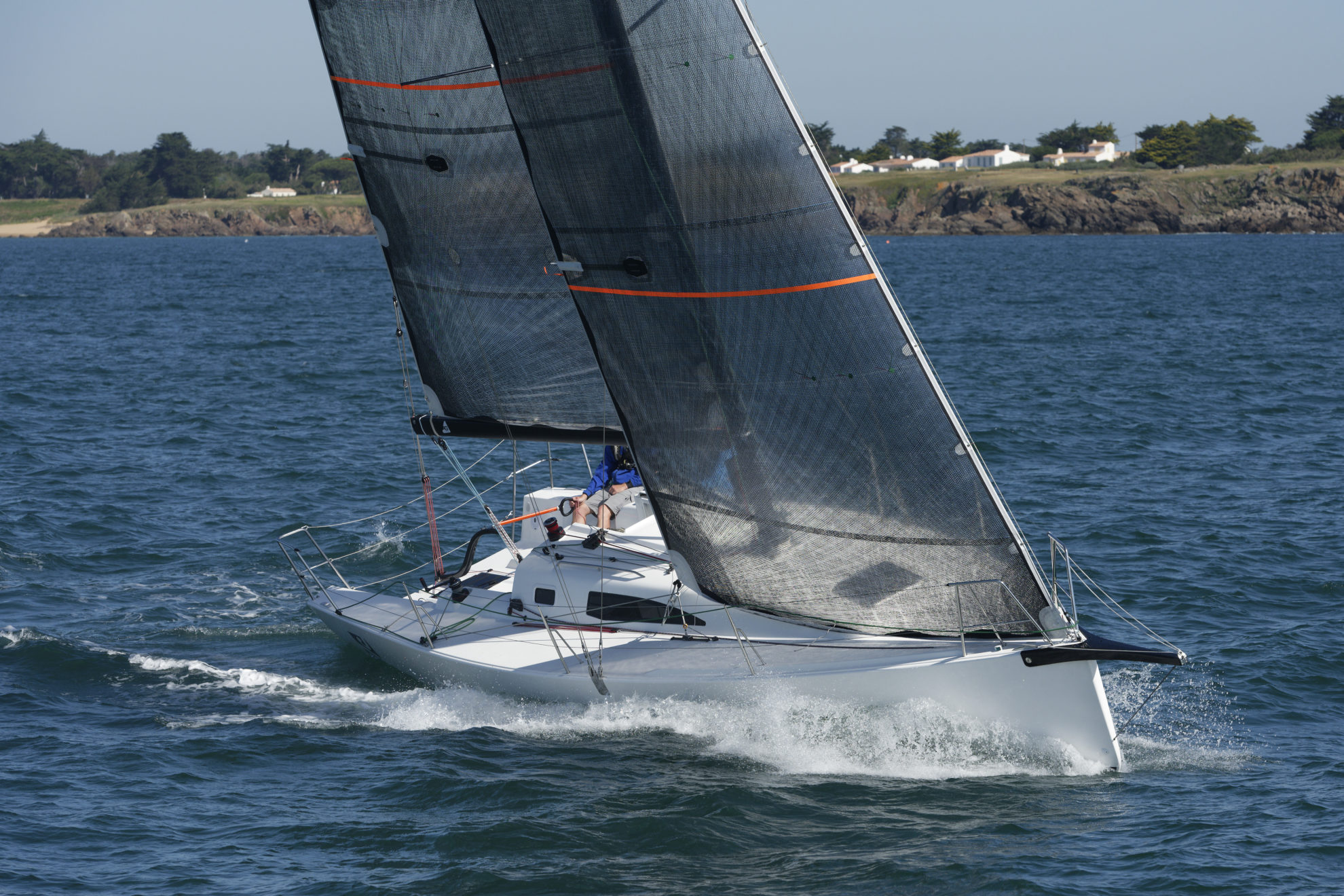
Le plastique, c’est fantastique* et pas très compliqué. N’importe qui ou presque peut s’improviser constructeur de bateaux. De même qu’avec un point d’appui on peut soulever la Terre, avec un bon moule on peut fabriquer une carène. Souvenez-vous d’Éric Tabarly, recyclant la coque pourrie de son vieux Pen Duick pour créer un moule avant d’appliquer lui-même de la résine sur sept couches de tissus de verre et ressusciter ainsi son merveilleux plan Fife de 1898
Durant des décennies, la technique de construction des bateaux en fibre de verre est restée la même : une fois les tissus disposés à l’intérieur du moule, on leur donne leur rigidité en appliquant la résine polyester au rouleau, façon peinture murale. Il suffit ensuite d’attendre que la résine polymérise (durcisse) pour que naisse une coque.
Bien adaptée à la construction en série, relativement bon marché, simple à mettre en œuvre et n’exigeant pas de compétences très pointues, l’application dite « au contact » a aussi ses inconvénients : impossible de doser précisément et uniformément la quantité de résine appliquée comme d’éviter la formation de bulles d’air, en dépit du recours au rouleau ébulleur. Les coques et ponts ainsi construits présentent des devis de poids inégaux et parfois une homogénéité aléatoire. D’où, en cas de mise en œuvre trop approximative, des problèmes de vieillissement prématuré, voire de délaminage, quand les tissus se décollent. Sans oublier la question de la pollution, la catalyse de la résine polyester à l’air libre émettant du styrène, composé particulièrement toxique.
Pour répondre aux exigences très élevées de l’aéronautique, des ingénieurs américains inventèrent -et brevetèrent- une autre technique, nettement plus sophistiquée : le Scrimp process (Seemann Composites Resin Infusion Molding Process). Ils eurent l’idée de diffuser la résine sous vide en utilisant une bâche en plastique épousant au plus près la forme de la pièce à construire.
Le chantier américain Tillotson Pearson Inc., alors l’un des leaders de la construction de voiliers outre-Atlantique, décida d’appliquer ce procédé à la construction d’un monotype au succès phénoménal, le J 24.
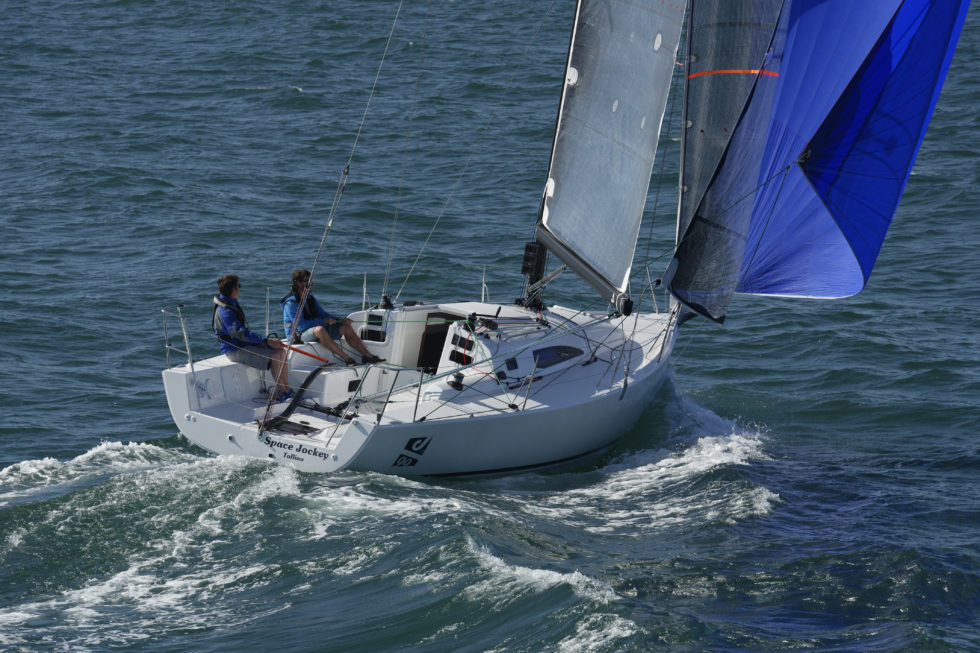
En Europe, un éphémère constructeur des Sables d’Olonne, désireux de produire un catamaran de 24 mètres à moteur au devis de poids optimisé décida d’acquérir la licence du Scrimp Process (pour 25 000 $, formation des techniciens comprise). Hélas ce pionnier ne parvint à vendre qu’un seul exemplaire de son King Cat et ne tarda pas à couler.
Les salariés de King Cat, leur savoir-faire, leur outillage et leurs locaux n’attendaient qu’un repreneur. Excellent régatier, futur chef d’entreprise créatif et audacieux, Didier Le Moal avait rencontré Jeff Johnstone, fils d’un deux frères fondateurs de l’Américain J Boats, en juillet 1994 à La Rochelle. Rencontre féconde : six mois plus tard, Le Moal créait J Composites, pour développer la construction sous licence des J, aux Sables d’Olonne. Ce chantier fonctionne depuis en étroit partenariat avec J Boats USA.
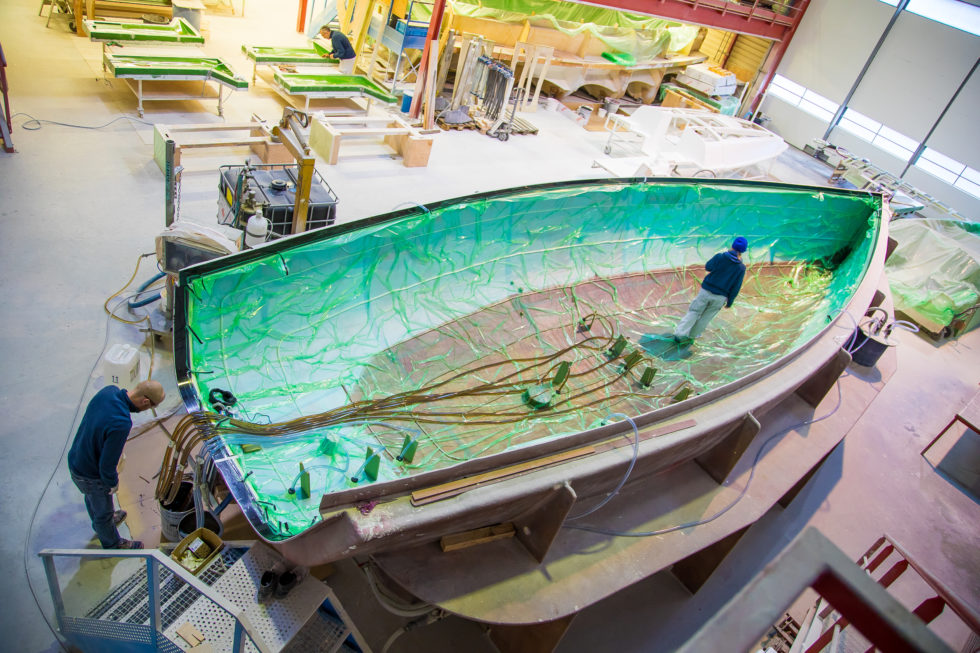
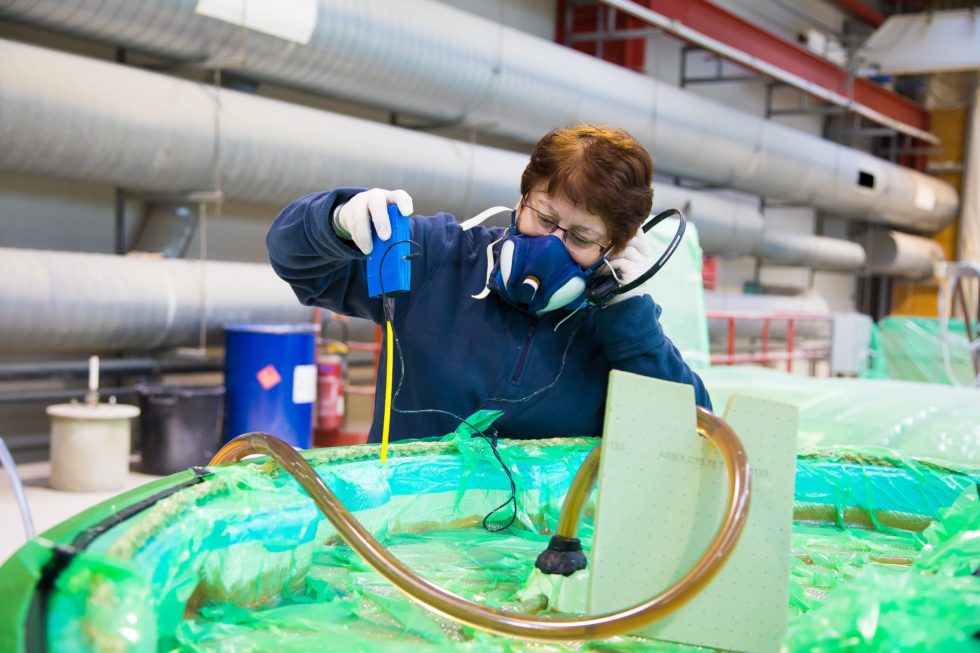
A l’aube du XXIème siècle, Le Moal et son équipe avaient défini un nouveau « cruiser-racer » de onze mètres, conforme aux attentes des clients européens. Pour construire en France cette remarquable unité de course-croisière, dessinée comme tous les J modernes par Alan Johnstone, les animateurs de J Composites estimèrent que l’infusion s’imposait.
Ils entendaient en effet proposer un bateau rigide et léger, aussi solide que performant. Au tout début, les pionniers de J Composites sous-traitèrent la construction de cette future star des plans d’eau à l’ex-atelier de King Cat qui fut rapidement intégré au nouveau chantier.
Les spécialistes de King Cat introduisaient la résine sous vide, au sein d’une toile d’araignée de tuyaux diffuseurs et de points d’injection implantés en une quantité d’emplacements stratégiques. Ils recouvraient le tout d’un film plastique souple et étanche, la « bâche à vide » dont les bords étaient collés au moule. Une pompe à vide permettait alors à la bâche de compresser les tissus tandis que la résine, aspirée par le vide, imbibait lentement et uniformément toute la coque. La quantité de résine utilisée était ainsi contrôlée au gramme près. J Composites produisait des coques plus légères, plus homogènes et plus rigides. Idéales pour garantir d’excellentes performances à un voilier utilisable en régate comme en promenade.
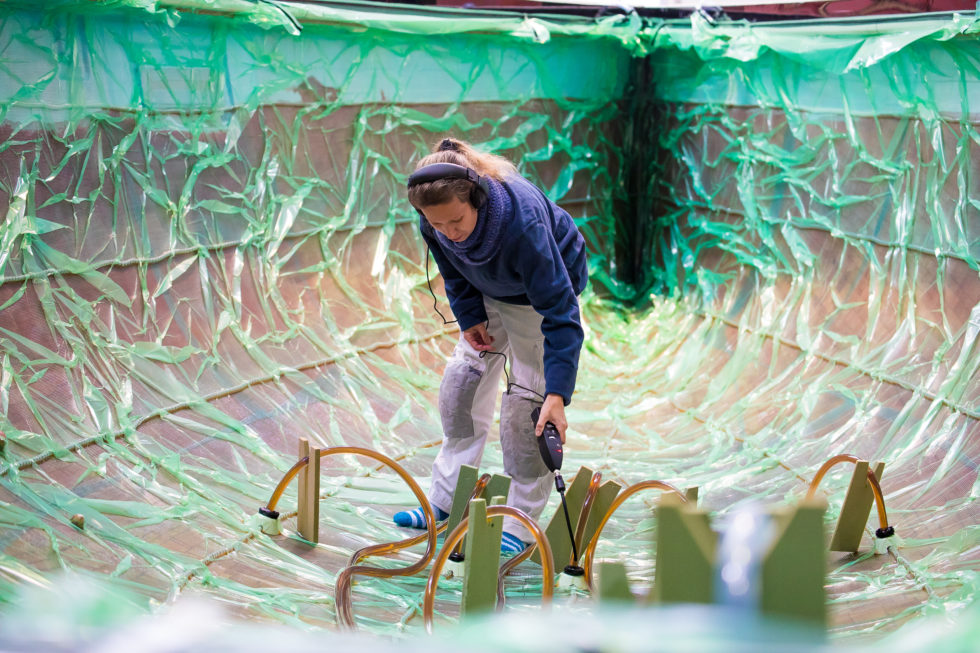
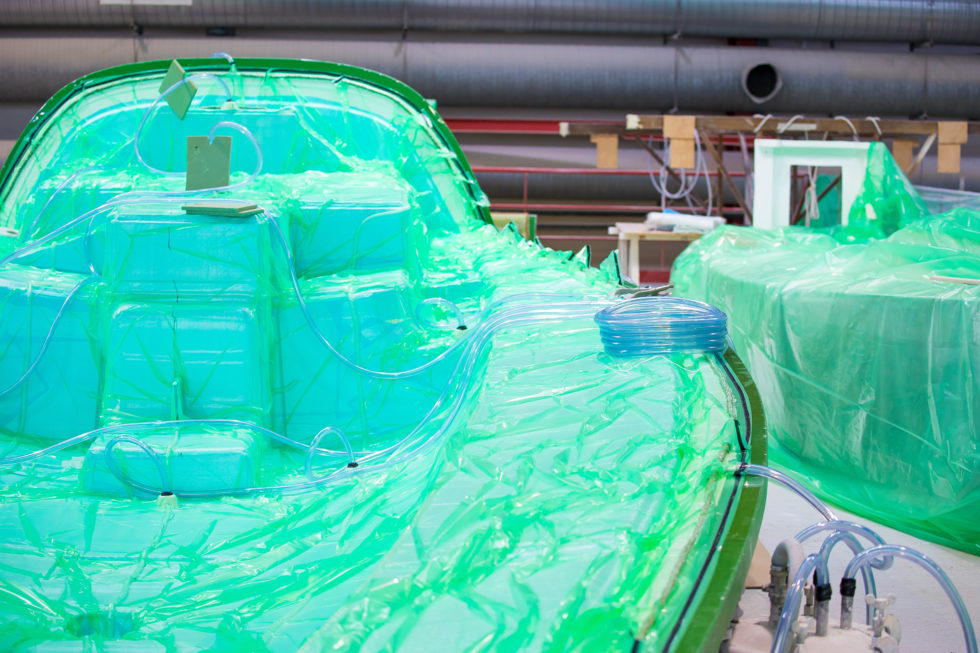
Avec sa coque en sandwich balsa, le J 109 devint ainsi le premier monocoque de série construit en infusion en Europe. Le numéro un sortit du chantier en 2001. Le J 109 ne tarda pas à faire un malheur en régate. Et dans les carnets de commande : au total, ce précurseur de toute la gamme J moderne s’est vendu à 400 exemplaires. Il fut le premier maillon d’une famille de voiliers remarquables, fabriqués aujourd’hui en sandwich mousse à cellules fermées selon une technique d’infusion qui n’a cessé de progresser.
Remarquons que dès la fin des années 90, les constructeurs de catamarans de croisière, alors en pleine croissance, s’étaient eux aussi tournés vers l’infusion. Tandis que ces unités se chargeaient de plus en plus d’équipements domestiques pour faciliter la vie à bord, il devenait crucial d’alléger les coques.
« Telle est la raison, explique Bruno Belmont l’un des pères de l’épopée Lagoon, qui nous a naturellement poussés à recourir à l’infusion : il n’était pas si difficile que cela de contourner le brevet du Scrimp. »
Parce que la courbe d’apprentissage de l’infusion peut être longue, parce qu’elle exige une mise en œuvre délicate, parce qu’elle utilise plus de consommables -les bâches ne sont pas récupérées- cette construction « premium » fut un temps l’apanage d’entreprises petites ou moyennes. Les grands groupes, en revanche, recouraient à l’injection, procédé similaire dans lequel la bâche est remplacée par deux moules « en dur » à l’intérieur desquels se diffuse la résine. Le groupe Bénéteau, par exemple, utilise l’injection pour la fabrication du pont de ses modèles.
Reste que l’infusion est en moyenne 30 % à 40 % plus onéreuse que l’application au contact, ce qui se répercute bien évidemment dans le prix des bateaux neufs. En contrepartie, les unités construites en infusion vieillissent bien et tiennent mieux la cote de l’occasion que les autres… Dans les années 2000, seuls quelques chantiers bretons spécialisés dans les monocoques de performance, tels JPK Composites, Pogo Structures ou IDB Marine, optèrent à leur tour pour cette technique. Mais les constructeurs de catamarans de croisière, comme on l’a vu, ne les avaient pas attendus. Quant au chantier de monocoques Dufour, il ne devait pas tarder à les rejoindre. Spécialisé dans les vedettes à moteur de petite et moyenne dimension, le Charentais Ocqueteau s’est aussi converti à ce procédé.
En 2016, le brevet du Scrimp process est tombé dans le domaine public. L’infusion a de beaux jours devant elle.
*Voir l’article « Innovation », dans la section 1950-1960
https://museedelaplaisance.com/collection/le-plastique-fantastique
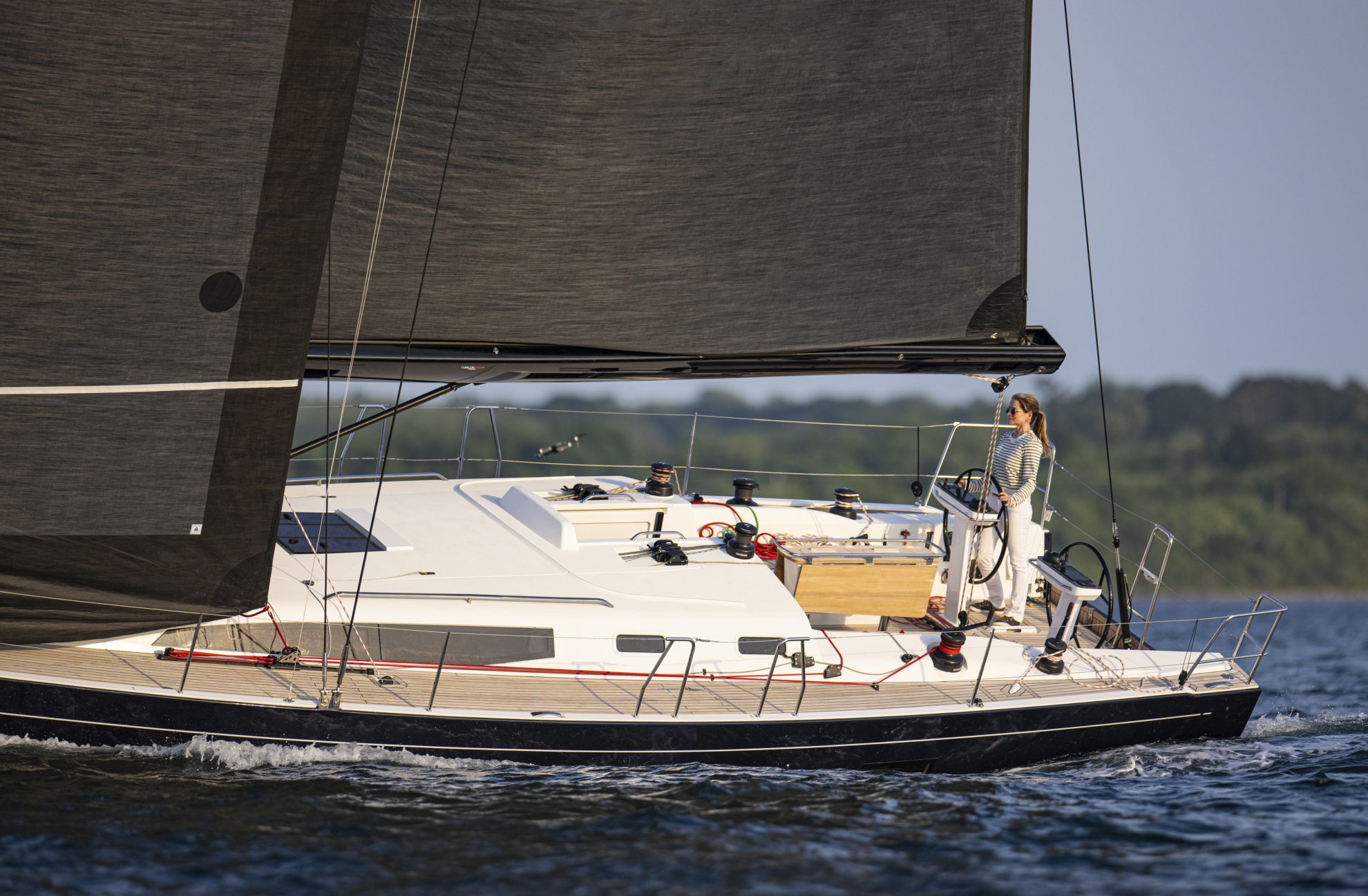